Ryan Smith
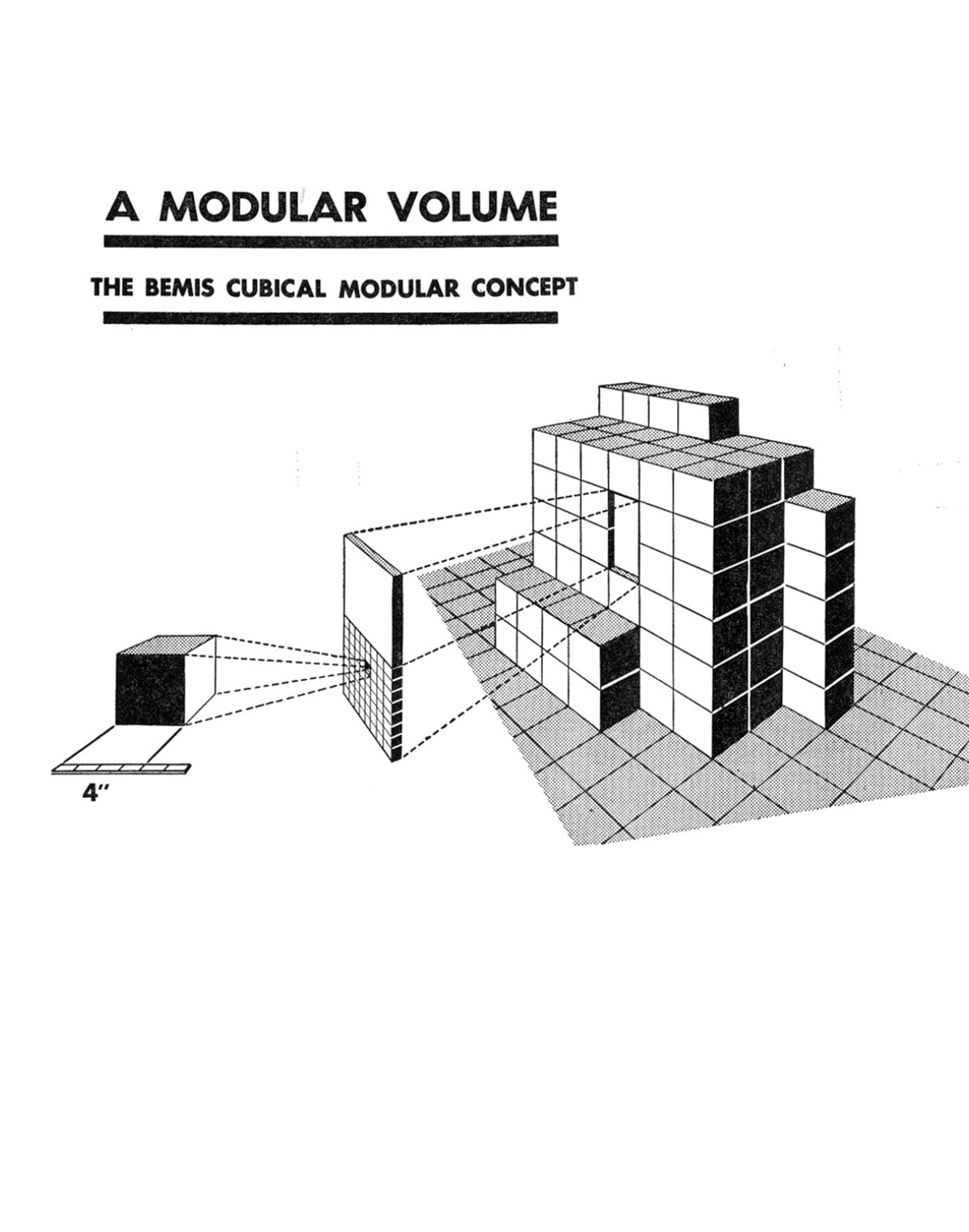
Prefabrication is misunderstood. For architects, it is often associated with the banality of social housing projects or low-quality mobile homes. Conversely, prefabrication, or its shortened popular culture name, “prefab,” is a term the public uses to reference high-end modernist modular residences promoted by Dwell Magazine.2 The truth is prefabrication is both of these things and more. Prefab is a mode of production, utilizing the principles of manufacturing in construction. It does not know a particular style, form, or degree of quality. An example of architects’ oversimplification prefabrication can be demonstrated in Chris Knapp’s recent sentiments on prefab. He states,
Mass production is the realm of the industrial designer and the process engineer—so let them maintain claim over that territory. The bespoke is the true specialty of the architect and the contemporary profession has more facility than ever to implement difference in the most intelligent of ways.3
The danger of conflating the terms “prefabrication” and “mass production” is that this ignores the complexity and reality of the expansive proliferation of off-site fabricated and constructed components, levels of customization and factory finish, and lean on-site delivery techniques that comprise the maturing field of prefabrication in design and construction. A recent survey demonstrated that prefabrication is being used in one form or another on more than 90 percent of projects built nationally from structure, enclosure, interior, and mechanical components to full volumetric modules and service pods.4 Prefabrication is not the antonym of bespoke any more than mass production is the opposite of implementing difference. Prefab is here to stay, more present than it has been at any time in history. We would do well not to ignore this growing field, but to have it become an integral part and even lead in the delivery of manufactured construction—prefabricated design and assembly—seeking unique customization and employing standardization as appropriate.
Historical Prefabrication
Prefabrication began as a social movement emerging from the Great Depression in the 1930s. During this era of deflation, the promises of prefab were proclaimed widely when the July 1932 edition of Fortune called prefabrication “the greatest commercial opportunity of the age.”5 Consistent with this era, the 1932 Merriam-Webster definition of prefabricate is “to fabricate parts at a factory so that construction consists mainly of assembling and uniting standardized parts.”6 Etymological research shows that prefabricate was first used in 1919 through an amalgamation of pre + fabricate. Fabricate dates to the fifteenth-century Latin Fabricatus, the past participle of fabricare, meaning “to fashion, make, build.” Prefab (ca. 1937) is short for prefabrication, a noun, and prefabricated, an adjective, as in “prefab housing,” which became commonplace in 1942.7 Significant advances and progress in prefabrication were made during the period following World War II.
Industrialized housing and prefabrication were discussed in the context of affordable housing during the 1950s and 1960s. However, prefabrication fell out of favor as a larger subassembly, panelized, and modular solution until the late 1960s. In its place was the development of other components that became automated and optimized, including prefabricated doors and jambs, windows, roof trusses, and so on. In 1969, George Romney, the new secretary of Housing and Urban Development, had experience with the advances in mass production and automation. He initiated Operation Breakthrough, a program encouraging large national corporations to enter the housing industry by provision of a federally assembled mass market. The program focused on the R & D of new systems and technologies for housing, and scaling prefab housing in terms of market, codes, and the creation of pathways to overcome other impediments to realizing prefab.8
Records indicate that 236 companies entered the competition for Operation Breakthrough, and twenty-two were selected to develop their housing systems and produce prototypes on eleven urban sites across the country (Figure 1). Operation Breakthrough ran from May 1969 to January 1973, when the Nixon administration placed a moratorium on housing funds. This cut the program short of Phase III, during which the prototypes were to be scaled to volume production.
Operation Breakthrough brought with it research efforts at universities. For example, the University of California, Berkeley, became home to the Architecture Experiment Laboratory that called for industrialization of building components and the integration of software. MIT held a series of symposia focused on the topic of prefabricated housing.10 The R & D efforts of the companies and universities fostered a more sophisticated vocabulary surrounding prefabrication, including nomenclature such as prefab housing,11 industrially produced housing, industrialized housing, manufactured housing, and mass-produced housing. This era marked the emergence of our modern prefabrication language vernacular, including terms such as systems building,12 service core, precast, frame and infill, components, subsystem, panels, and, seemingly the most widely accepted and durable word in the American prefab parlance, modular.13
Modular Definitions
The Oxford Dictionary’s definition of the word module indicates that it evolved from its sixteenth- and seventeenth-century meanings, “general uses relating to extent or relationship” and “technical uses relating to measurement and proportion.”14 Le Corbusier used the term Modulor to describe his system of measurement based on the anthropometric proportions of the height of a man with his arm raised. It was a way to compromise between imperial and metric systems of measurement to provide what Le Corbusier described as a harmonious scale to be applied to shipbuilding, civil engineering projects, and even residential construction.15
By the mid-twentieth century, however, the Oxford English Dictionary’s definitions of module and modular reflected industrialized technology and language. It reads, “8. A length chosen as the basis for the dimensions of the parts of a building, esp. one to be constructed from prefabricated components, all the dimensions being integral multiples of it.”16 Oxford credits Albert Farwell Bemis with the origin of this more contemporary definition of module, citing his 1936 book, The Evolving House.17
Patent filings as early as 1932 show that Bemis believed in a system of coordination that combined both standardized dimensions and “components of a larger or more complex system” and “any of a series of independent units or parts of a more complex structure, produced to a standard design in order to facilitate assembly and allow mass production.”18 Here modules become modular construction, defining our contemporary understanding of the word (Figure 2). Russell summarizes:
This explains the modern societal understanding that has moved beyond Le Corbusier’s definition of modular as a system of measurement and proportion into complex systems and interchangeability of elements. The computer industry emerged during the 1970s with IBM System/360 using the word modularity to describe its own interchangeability and flexibility of its servers for business (Figure 2).20 Today the manufacturing sector uses the word modularity, including component-sharing modularity, component-swapping modularity, cut-to-fit modularity, mix modularity, bus modularity, and sectional modularity, in connection with mass customization (Figure 3).
Architecture today is seemingly using an antiquated definition of module, modular, and modularity. The discipline uses modular to refer to the standardization from Le Corbusier. We also describe the construction volumetric unit of Bemis as modular (i.e., permanent modular construction or relocatable/temporary modular). However, modular today is much more. Modular refers to the functionality, flexibility, and customization opportunities associated with contemporary production methods—the factory work proper with its capabilities in CNC and automation, hybrid handwork, and lean station manufacture. Architectural production today is able to achieve economies of scope (quality and effect) when appropriate in addition to the traditional advantages of economies of scale that accompany Fordist mass production.
Production Theory
On both extremes of the production spectrum, buildings and their fabrication may be standardized or custom. However, these terms do not capture the complexity of manufacturing and fabrication scope. Four terms have emerged in the manufacturing industry to describe the levels of prefabrication completion and associated effort that can be expended in manufacturing. These terms and definitions aid in helping architects understand the boundary of the building project that is being discussed and developed, creating a new language bridging between design and construction at the moment of fabrication. These terms of manufacturing are explained in the book Prefab Architecture: A Guide to Modular Design and Construction21 and include Made-to-Stock, Assembled-to-Stock, Made-to-Order, and Engineered-to-Order.
• Made-to-Stock (MTS): MTS products are best handled through inventory replenishment strategies. In order to keep inventory replenished, manufacturers have used standardization, or reducing complexity and increasing repetition. Supplier-managed inventory has proven successful for some companies and projects, where suppliers take on the job of determining requirements, and maintaining and distributing materials. Examples of MTS products include warehoused building goods such as lumber, wood, steel, and aluminum sections, ceiling tiles, and panel material such as gypsum board or plywood.
Some products have become so specialized that design service providers have emerged to fill the market need. They include engineers of ETO products. They are the outsourced companies that produce steel detailing, specialized curtain wall consultation, tilt-up providers, modular dealers, and so forth. Another method by which ETO products are procured is in the form of specialist coordinators. These subcontractors do not actually design or manufacture prefabrication components but provide a service of bringing together design, supply, and fabrication. More and more subcontractors are moving to this model, offering their services, but with no ability to manufacture. Because of this specialization, smaller manufacturing and construction firms (the majority in the United States can be described as such) can perform the production in a factory and the installation work on-site (Figure 4).
Conclusion
There is a movement to create a unique vocabulary specific to prefabrication, its products, and its processes of delivery. This will occur organically out of the maturing of the research and practice of the prefab field. More recently, Build Offsite, a trade association in the United Kingdom,24 and the National Institute of Building Science, Off-site Construction Council, a knowledge management organization in Washington, DC,25 have published peer-reviewed glossaries to enumerate and define the terms in the prefabrication sector. Sweden, a more sophisticated prefabrication market, has developed a specific industry-wide language concerning subassembly sequencing in particular for the residential construction industry. Disciplinary knowledge depends on a common language.
This review demonstrates our historical and contemporary understanding of prefabrication from the perspective of the traditional harbingers of building delivery: designers (architects and engineers) and constructors (general contractors, site subtrades). Herein is a call for framing prefabrication from a different perspective, that of production—process and product—or manufactured construction. The review is intended to provide a more nuanced and intelligent way in which to study, understand, and discuss the extent and breadth of prefab as a growing domain of the architecture discipline. Architectural production is not standardized or custom; it is various levels of factory production that must be considered with regard to the specific project design and construction goals.
[1] R. E. Smith, “Connect Homes: Modular Housing Patent and Architect-Led Business Model,” Journal of Architectural Education 70, no. 1 (March 2016): 168–171.
[2] Dwell Magazine, led by then editor in chief Allison Arief, hosted a prefab housing competition with the results prototyped and published. The magazine then ran a series of issues on prefabrication history and future projections. It continues to promote the architect-designed modern modular through its online channels and sponsorship.
[3] C. Knapp, “The End of Prefabrication,” Australian Design Review, October 18, 2013 (http://www.australiandesignreview.com/features/35295-the-end-of-prefabrication).
[4] R. E. Smith, Report of the Results of the 2014 Off-Site Construction Industry Survey (Washington, DC: National Institute of Building Sciences, 2014) (http://c.ymcdn.com/sites/www.nibs.org/resource/resmgr/OSCC/NIBS_OSCC_2014Survey.pdf).
[5] B. Alfred and H. Sandbank, The History of Prefabrication (New York: Arno, 1972), 7.
[6] Merriam-Webster Dictionary, 1932.
[7] D. Harper, “Prefabricate,” in Online Etymology Dictionary, 2016 (http://www.etymonline.com/index.php?allowed_in_frame=0&search=prefabricate); and R. K. Graff, Prefabricated House (New York: Doubleday, 1947).
[8] B. J. Sullivan, Industrialization in the Building Industry (New York: Van Nostrand Reinhold, 1980), 21–37.
[9] “Operation Breakthrough—Phase I, Design and Development of Housing System,” U.S. Department of Housing and Urban Development, U.S. Government Publication; and “Operation Breakthrough: Lessons Learned about Demonstrating New Technology,” PSAD-76-173: B-114860, November 2, 1976.
[10] Alfred and Sandbank, The History of Prefabrication (note 5), 7; and “Industrialized Housing Forum,” School of Architecture, Massachusetts Institute of Technology, January 1950.
[11] Royal Institute of British Architects, The Industrialisation of Building: an appraisal of the present position and future trends, (London: Royal Institute of British Architects, 1965).
[12] Systems Building News, vol. 3, no. 1 (Atlanta: W.R.C. Smith Publishing Co., 1974).
[13] John G. Blair, Modular America: Cross-Cultural Perspectives on the Emergence of an American Way (New York: Greenwood, 1988).
[14] Oxford English Dictionary, 3rd ed., s.v. “module, n.” (http://dictionary.oed.com).
[15] Le Corbusier, The Modulor: A Harmonious Measure to the Human Scale, Universally Applicable to Architecture and Mechanics (Basel and Boston: Birkhäuser, 2004). This work was first published in two volumes in 1954 and 1958.
[16] Oxford English Dictionary, 3rd ed., s.v. “module, n.” (note 14).
[17] Albert Farwell Bemis was an industrialist and established the Bemis Foundation that performed research into industrialized building production. Bemis and his foundation published many works, some after his death in 1936. His most notable was A. F. Bemis, The Evolving House, vol. 3 (Cambridge, MA: MIT Press, 1936). This work is clarified in B. Kelly, The Prefabrication of Houses, A Study by the Albert Farwell Bemis Foundation of the Prefabrication Industry in the United States (The Technology Press of the Massachusetts Institute of Technology and John Wiley and Sons, Inc., New York, 1951. The body of work is archived in the Albert Farwell Bemis Foundation records 1926-1954 at the Massachusetts Institute of Technology, Cambridge, MA.
[18] A. F. Bemis, “A Modular Volume: The Bemis Cubical Modular Concept,” in Basic Principles of Modular Coordination (Washington, DC: U.S. Housing and Home Finance Agency, 1953), 5.
[19] A. L. Russell, “Modularity: An Interdisciplinary History of an Ordering Concept,” Information and Culture: A Journal of History 47, no. 3 (2012): 261
[20] Blair, Modular America (note 13).
[21] R. E. Smith, Prefab Architecture: A Guide to Modular Design and Construction (New York: Wiley, 2010), 122–124.
[22] S. E. Sampson, “The Unified Service Theory: A Paradigm for Service Science,” in The Handbook of Service Science, ed. P. P. Maglio, C. A. Kieliszewki, and J. C. Spohrer, Service Science: Research and Innovations in the Service Economy (New York: Springer Science + Business Media, 2010), 107–131.
[23] H. Lidelöw, L. Stehn, J. Lessing, and D. Engstrom, Industriellt hysbyggande (in Swedish) (Lund, Sweden: Studentlitterature, 2012).
[24] A. G. F. Gibb and M. C. Pendlebury, eds., Buildoffsite Glossary of Terms, 2nd ed. (London: Construction Industry Research & Information Association, 2006), 38 pp.; and National Institute of Building Sciences.
[25] “Glossary of Off-site Construction Terms,” http://c.ymcdn.com/sites/www.nibs.org/resource/resmgr/OSCC/GlossaryOffSiteConstructionT.pdf.
How to Cite this Article: Smith, Ryan. “Prefabrication.” JAE Online. April 27, 2016. http://www.jaeonline.org/articles/exhibit-reviews/prefabrication#/.